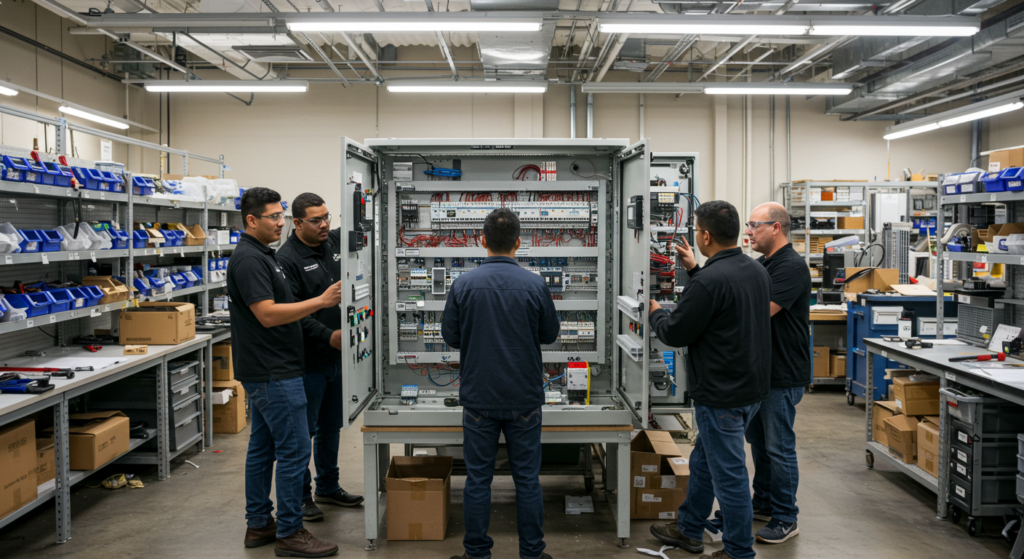
Exploring the Many Names and Benefits of Industrial & Commercial UL508a Custom Control Panels From AppliedGrayMatter.com
Industrial and commercial control panels are the unsung heroes of modern automation, energy management, and manufacturing systems. Known by many...